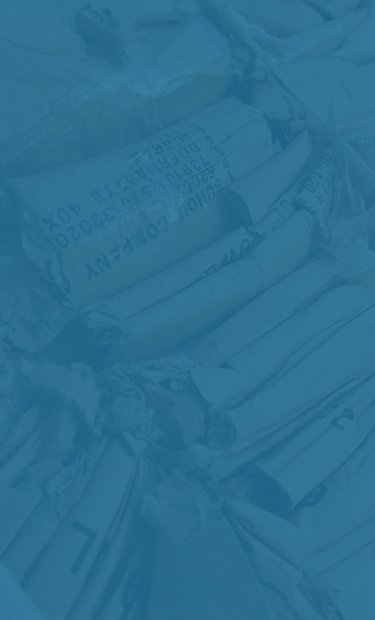
What makes a hydraulic baler distinct from a pneumatic baler?
Our Guide will help you distinguish between hydraulic and pneumatic balers used for recycling.
Both hydraulic and pneumatic balers are utilized for recycling
When deciding to add a recycling baler to your commercial property, you will have to choose between hydraulic and pneumatic balers.
These machines perform essentially the same function: they compress recyclable materials such as paper, cardboard, and plastic into dense blocks (bales) that are readily transportable and recyclable.
Each machine has a power source and presses materials using that power.
What then is the distinction?
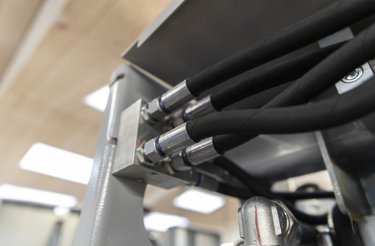
Pneumatic
The power source for pneumatic balers is compressed air. Air is pumped into the upper cylinder to generate pressure that presses the pressing plate downward. The pressure immobilizes the pressing plate without additional use of power.
Pneumatic balers operate purely on compressed air; no electrical components are present.
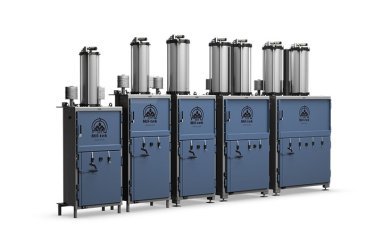
Hydraulic
Hydraulic Balers pump hydraulic fluid with an electric motor. The hydraulic oil generates pressure in the actuators, which forces the pressing plate downward.
Hydraulic balers are powered by an electrically-operated motor.
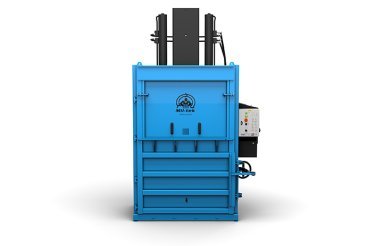
“Pneumatic Balers utilize pressurized air to compress the pressing plate. Hydraulic Balers deliver hydraulic oil to the pressing rams in order to apply pressure to the pressing plate”
Additional considerations pertaining to pneumatic versus hydraulic balers
These two categories of balers can help your business effectively manage waste. Each has advantages that are more suitable for one business than another. Typically, it depends on the specific needs of the business.
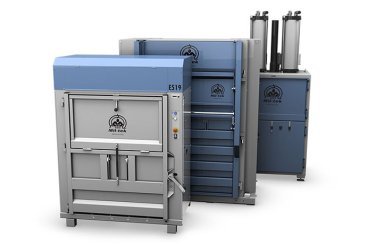
Here are some additional considerations when contrasting hydraulic and pneumatic balers:
- Volume – Hydraulic balers are preferable for high volume (approximately one ton per week or more)
- Size – Pneumatic balers are typically compact and better adapted for confined work areas
- Noise – Because hydraulic balers are typically quite loud, they are frequently installed away from the production process
- Noise – Because pneumatic balers are calmer, they are frequently installed near the production process
- Maintenance – Both pneumatic and hydraulic balers require annual maintenance, with pneumatic balers requiring less due to the absence of electrical components
- Source of Power – Pneumatic balers can be plugged directly into existing air lines. If not, a compact compressor is needed. Compressed air is used to secure the pounding plate of a pneumatic baler once it has been lowered. Hydraulic balers require constant power to maintain constant pressure
- Strength – The high pressure of the hydraulic oil exerts a greater downward force on the material than compressed air, but at a greater cost in terms of power
- Hygiene – Pneumatic balers are more suitable for use in food production facilities because they reduce the risk of contamination.
Do you have any further questions?
By managing waste more effectively, your company may save time, space, and money. Let us assist you in finding the solutions.
Once you submit the form, one of our local employees will contact you to offer assistance.