LEANcompacting implemented at HydraSpecma
Staff can purely focus on doing tasks that add value to the business, rather than taking the cardboard and plastic waste for an unnecessary walk
Mil-tek LEANcompacting at HydraSpecma
Hydra Specma reduced internal truck transportation by 75% and saved 8 hours per week by implementing a LEAN and sustainable solution to their waste handling processes.
0%
LEAN production areas
Hydra Specma are a well-reputed Danish company employing around 300 staff. Hydra are supplying various components to the industry in the broadest sense but has 3 specific focus areas, which are industry, wind and offshore.
At Hydra the production areas are all very LEAN, and it is obvious that they have a very LEAN approach to their day-to-day business – This is however being challenged a bit, as the operations are spread out across 3 separate buildings, as Hydra has expanded over the years.
A bi-product of this growth is that their waste handling has been somewhat difficult as they have been forced to transport waste from these buildings to the outside waste collection area. Waste was collected in cages around the facility and then taken by truck to the outside waste area.
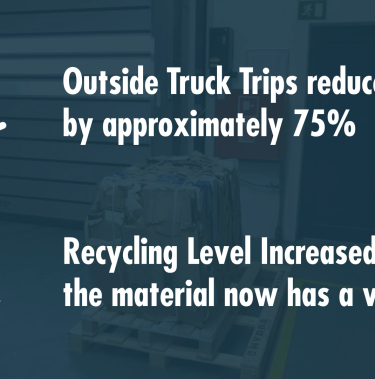
Value stream mapping with GPS
Mil-tek assisted in a value stream mapping exercise on Hydra’ internal waste transport with the help of GPS technology. It uncovered that the waste wagon was doing around 50 km. pr. a week and going out of the production buildings 30 times per day on average. It was also calculated that approx. 8 hours per week was spent at the large outside compactor for manually loading the waste from cages to the compactor.
For some of these cages in the unpacking area, which was closer to the outside waste area – the cages were transported outside by hand. Then unloaded manually. And then finally returned empty to the again unpacking area. All in all an unhandy process for staff, which Hydra also recognized and wanted to find an improved solution for.
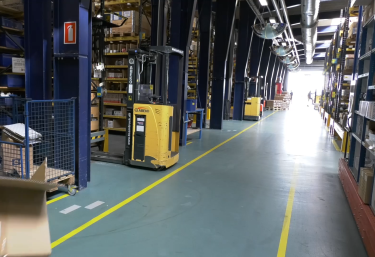
The right approach
Hydra had a very proactive and forward-thinking approach to this challenge and was interested in “reversing” this scenario to avoid all the outside trips with waste.
They were looking for a solution to make localised waste areas instead of the traditional single waste collection point. Further to this, they had a great interest in improving their green accounts and making sure as much waste as possible was recycled.
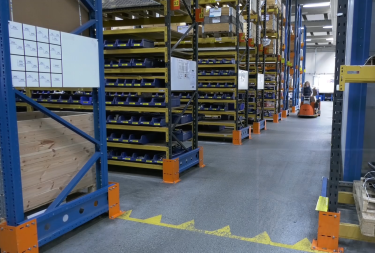
Simple to use
Mil-tek has since then supplied a variety of solutions that fits the need at Hydra.
In 2 of the 3 production areas, electrical Mil-tek solutions have been put in place, to handle large, heavy cardboard packaging streams.
Now, staff in these areas only have to feed these solutions and empty them once or twice a week. The Mil-tek solutions are simple to use, meaning that all staff has the ability to load and operate.
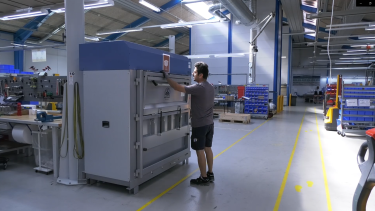
No unnecessary walks
In the unpacking area, a range of air-powered Mil-tek solutions has been connected to the existing airline installed, and are now handling all the cardboard and plastic waste that is being generated when unpacking goods coming in from sub-suppliers.
Here, every unpacking station has a dedicated Mil-tek solution for cardboard and a bag stand for plastic waste, so the staff can purely focus on doing tasks that add value to the business, rather than taking the waste packaging for an unnecessary walk.

Have a question?
Get in touch today to learn more about how Mil-tek can help your business save time, space and money by better handling waste
Get info about a product or have a chat with one of our local reps. Let us know what you need so the right person can get in touch