LEAN Waste Management
A Lean approach to waste management reduces the number of non-value-adding material handling processes. By increasing efficiency, lean waste management saves businesses time, space, and money.
Ineffective refuse management methods
It is common practice in many businesses to collect waste and recyclable materials, such as cardboard and plastic, in tiny containers located throughout the facility. These are depicted as tiny blue dots in the image on the right.
The waste must then be collected and transported multiple times a day to one or more outdoor containers, where it must be further sorted and processed by folding or cutting before being reloaded into a container or compactor.
Consequently, the productivity is interrupted and inefficient. Particularly when material is transported by Fork Lift Truck (FLT), there is a greater likelihood of incorrect sorting and a higher risk of internal catastrophes.
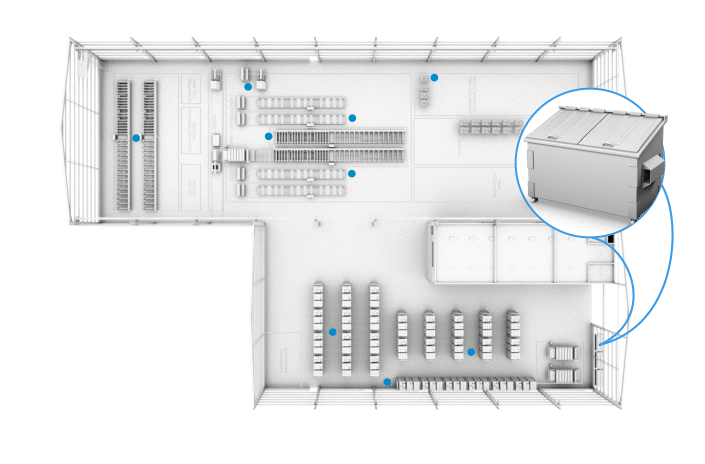
Standard outdoor waste containers have a number of drawbacks
There are a number of disadvantages associated with the use of external waste containers for waste collection by businesses:
• Considerable time lost in transporting materials to the external container area and additional loading time
• Uncompacted cardboard and plastic EPS (Polystyrene) waste space and necessitate additional containers or costly collection fees.
• Constant collection expenses: the container is emptied whether or not it is full.
• Incorrect material in the incorrect container! Incorrect classification results in added expenses
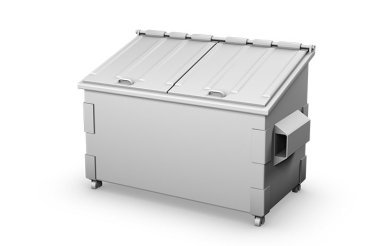
The Lean methodology entails streamlining workflows by eliminating unnecessary processes, minimizing internal and external travels, and implementing continuous improvements.
Lean processes are prevalent in production settings, but they can also be utilized to great effect in other industries.
Benefits of Lean Waste Administration
When customizing waste solutions, Mil-tek applies Lean principles. With a waste management solution based on Lean principles, our compressed air-driven waste compactors are placed as close as feasible to the unpacking area, as depicted in the image on the right.
The waste can then be dealt with promptly, directly in a cardboard baler or plastic baler, without the need to fold it or “walk with it” to a container. Up to 90% of the refuse is compacted in the baler. When it signifies a full bale, it can be emptied quickly and safely. The bales can be readily stored and collected later for recycling.
The outcome of Lean waste management is a significantly more efficient work flow, in which you save significant quantities of time and space on your waste management, as well as money on containers and collections.
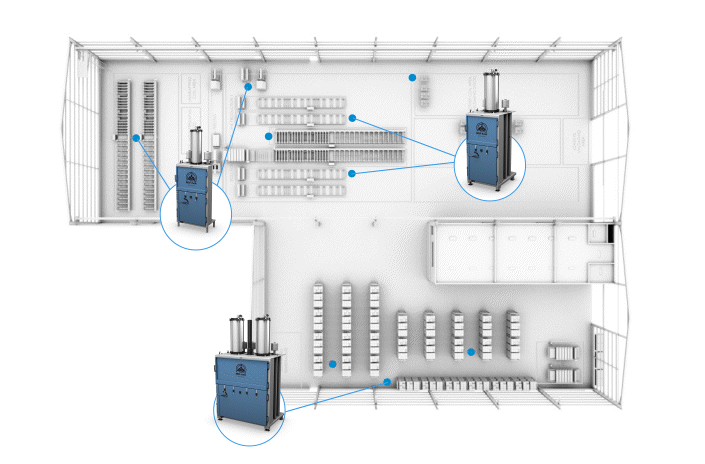
Lean waste reduction reduces usage of forklift trucks
Forklift truck driving-related workplace incidents happen often, and they can have devastating outcomes. If there is a mix of vehicle and pedestrian traffic, the danger of accidents increases. Clutter in the transport area makes the situation much worse.
By compacting waste at the source, a lean approach to waste management greatly decreases the requirement for forklift truck operation and raises safety standards.
Ten times fewer truck journeys
Your travels can move ten times as much stuff when you condense the material before moving it. This many fewer trips means fewer accidents, increased productivity, and cost savings.
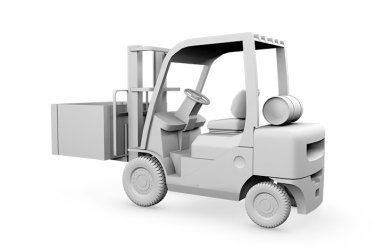
Four crucial Lean principles
Here, you may learn about four fundamental Lean principles that Mil-tek largely applies while creating a custom waste solution for you.
Continuous improvement, or “Kaizen”
It’s about incorporating the entire team in ongoing improvements. ‘Kaizen boards’ are frequently used in businesses to track the development of new Kaizen concepts that increase productivity.
“8 types of waste”
TIMWOODS! A great way to remember the 8 sources of waste: Time, Inventory, Motion, Waiting time, Overproduction Over-processing, Defects, Skills.
“Value Stream Mapping”
is the practice of mapping production flows or other processes in order to find areas where efficiency can be increased.
“5S” is a tool for establishing order and system
Sort, arrange in order, clean thoroughly, standardize, and exercise self-control. Working with 5S can help you enhance your workplace’s ergonomics, working conditions, quality, productivity, and employee wellbeing, among other things.
– A new ‘S’ has been added, the sixth: Safety: All of the aforementioned tasks must be completed in a secure working environment.
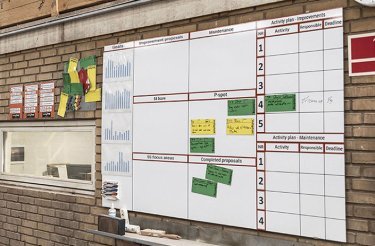
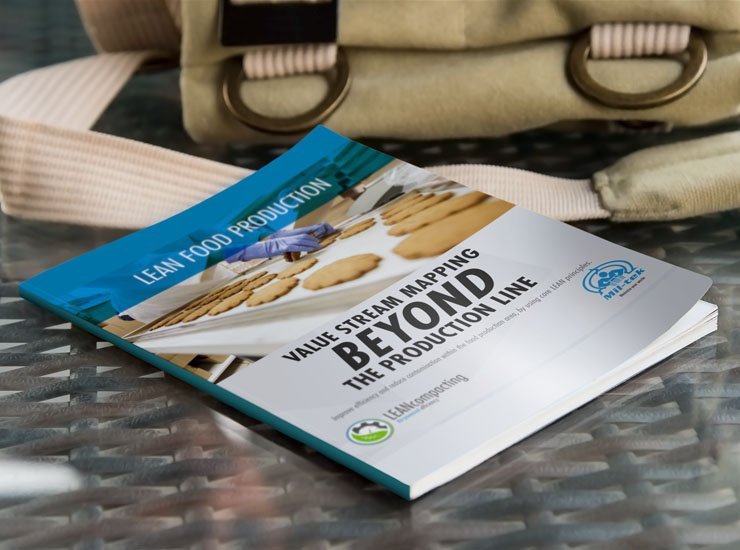
Interested in learning more Lean?
Have you started to wonder how you may improve your waste management using the Lean methodology and make significant savings and gains?
Contact us using this form, and we’ll get back to you right away.